Лазерная и плазменная резка металла отличия
Что предпочтительнее — плазменная или лазерная резка — зависит от марки и толщины разрезаемых металлов, от требований к точности реза и от финансовых возможностей заказчика. Эти факторы являются решающими, когда необходимо купить оборудование для резки металла. Комплектующие для лазерной резки должны быть качественными, а также доставлены вам в кратчайшие сроки и по минимальным ценам.
HYPOWER – символ высокой мощности, долгого срока службы расходных материалов для многих областей металлообработки, таких как сварка, плазменная, лазерная и газовая резка.
Обе технологии — извечные конкуренты (но не антагонисты!). Хотя, при определенных условиях, одна вполне заменит другую. Однако существуют случаи, при которых предпочтения отдаются лазеру или плазме.
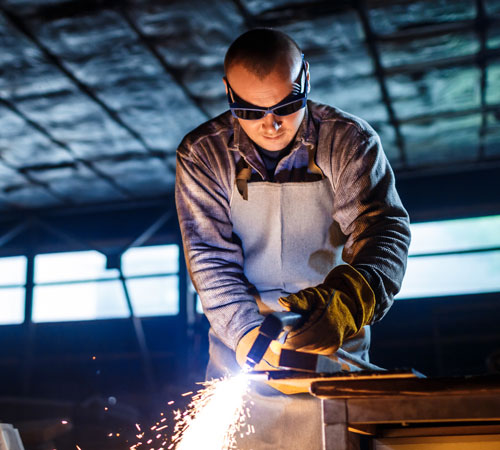
В чем суть лазерной и плазменной резки
При упрощенном рассмотрении лазерная резка осуществляется за счет сфокусированного лазерного луча, который, собственно, является режущим элементом. Во время непрерывной работы он раскаляет металл, в зоне своего присутствия, до температуры плавления. А расплавленный (по сути, жидкий металл), удаляется, подаваемой под высоким давлением, струей газа.
При сублимационной лазерной резке, под воздействием лазерного импульса, в зоне резания листовой металл испаряется.
В плазменной резке теплота, расплавляющая материал, возникает за счет генерации плазменной дуги. Удаление расплава также происходит за счет воздействия плазменной струи на жидкий металл.
Зависимость вида резки от толщины и марки раскраиваемого листа
Главным отличием лазерной резки металла от плазменной является точность перпендикулярности образуемых, в процессе раскроя, кромок и толщины прорезей. Так, сфокусированный лазерный луч делает линию реза более тонкой. А значит, меньшая зона листа нагревается в процессе резания. Это, в свою очередь, объясняет практически отсутствующую контурную деформацию получаемых заготовок.
Лазерная резка имеет приличную производительность при высочайшей точности получаемых деталей. Она обеспечивает идеальное вырезание небольших, но сложных по конфигурации фигур и высокую точность углов.
Однако данная технология наиболее эффективна при разрезании листов, толщина которых меньше или равна 6 мм. В этом случае на заготовках полностью отсутствует окалина, а кромки деталей идеально гладкие и прямолинейные.
При резке более толстых листов кромки скашиваются до 0,5 градусов. Поэтому диаметры отверстий, полученных лазерной резкой в нижней части, всегда имеют несколько больший размер, чем в верхней. Правда, качество реза и форма всегда остаются безупречными.
В отличии от лазерного, плазменное оборудование дает более качественный рез при обработке листов:
- из алюминия и его сплавов (толщиной до 120 мм);
- из меди (толщиной до 80 мм);
- из углеродистых и легированных сталей (толщиной до 150 мм);
- их чугуна (толщиной до 90 мм).
При этом для раскроя тонколистовых металлов (до 0,5 мм) плазменная дуга используется очень редко — из-за высокой температуры в зоне резания может возникнуть коробление контуров заготовок.
Кроме того, в процессе работы на таком оборудовании образуется конусность реза, варьирующая в пределах 3-10 градусов. Поэтому при вырезании отверстий в толстых металлах нижний диаметр меньше входного. Так, круг, вырезанный из 20 миллиметровой стали будет иметь разницу диаметров в 1 мм.
Ниже представлена сравнительная таблица функциональности лазерных и плазменных станков:
Параметры | Лазерная резка | Плазменная резка |
---|---|---|
Ширина реза | 0,2-0,375 мм | Ширина реза 0,8-1,5 мм |
Точность резки | ±0,05 мм | ±0,1-0,5 мм Зависит от степени износа расходных материалов |
Конусность | Менее 1° | 3° — 10° |
Минимальные отверстия | При непрерывном режиме диаметр примерно равен толщине материала. Для импульсного режима минимальный диаметр отверстия может составлять одну треть толщины материала. | Минимальный диаметр отверстий составляет 1,5 от толщины материала, но не менее 4мм. |
Внутренние углы | Высокое качество углов | Происходит небольшое скругление угла, из нижней части среза удаляется больше материала, чем из верхней |
Окалина | Обычно отсутствует | Обычно имеется (небольшая) |
Прижоги | Незаметны | Присутствуют на острых наружных кромках деталей |
Тепловое воздействие | Очень мало | Больше, чем при лазерной резке |
Производительность резки металла | Очень высокая скорость при малых толщинах. Заметно снижается с увеличением толщины металла, продолжительный прожиг больших толщин. | Быстрый прожиг; очень высокая скорость при малых и средних толщинах обычно с резким снижением при увеличении толщины. |
Отличие плазменной резки от лазерной по стоимости
Решая, что лучше — плазменная или лазерная резка металла, нужно понимать, что цена портальной плазменной установки в 5-6 раз ниже аналогичной лазерной. Однако при сравнении обоих видов оборудования следует учитывать не только стартовую стоимость, но и дальнейшие эксплуатационные расходы.
Сюда относят затраты на электроэнергию, вспомогательные газы и цену расходных материалов. Выбирая, что заказать — плазменную или лазерную резку металла, учтите, что в смету эксплуатационных расходов лазерной резки входят:
Стоимость газов:
- воздух или чистый кислород — для резки углеродистых сталей;
- азот — для получения заготовок из алюминия (его сплавов) и коррозионностойких сталей (например, нержавейки).
Энергозатраты:
- расходы на энергопотребление самой установки;
- электроэнергия для лазера и охладителя.
Расходные материалы:
- оптика (внутренняя и внешняя);
- сопла;
- фильтры.
Но ответ на вопрос: «Чем отличается плазменная резка от лазерной резки?» был бы не полным без знаний об эксплуатационных расходах на установку плазменной обработки. Поэтому продолжим детально изучать затраты на альтернативное оборудование.
При плазменной резке используют кислород или воздух. Электроэнергия расходуется исключительно на питание самого станка и создание плазмы. Что до расходных материалов, то их не больше, чем в лазерном оборудовании. Так, в этот пункт входят:
- сопло;
- электрод;
- защитный экран.
Такой показатель, как количество отверстий, приходящихся на одну заготовку, снижают часовую стоимость работы плазмы. В этом батле победу одержит лазер, поскольку сопла и электроды, используемые в плазменных агрегатах, рассчитаны на заданное количество прошивок и стартов.
Чем больше отверстий нужно сделать, тем выше эксплуатационные расходы на плазменный станок.
Резюмируя вышеизложенное, можно прийти к следующему выводу: сказать заочно, что выгоднее приобрести — плазменную или лазерную резку, невозможно. Но если требуется раскрой металла до 6 мм, а особенно с большим количеством отверстий, тогда в фаворе будет лазер. При резании материалов от 6 мм, покупайте плазменные аппараты с ЧПУ.
Особенности лазерной резки
Лазерные установки состоят из трех основных частей:
- Рабочей (активной) среды – источника лазерного излучения.
- Источника энергии (системы накачки), создающего условия, при которых начинается электромагнитное излучение.
- Оптического резонатора – зеркала, усиливающего лазерное излучение.
Металл разогревается на небольшом участке. Процесс раскроя может идти при температуре расплавления или испарения металла. Второй вариант энергозатратней и применяется только для тонких материалов.
Для облегчения работы в зону резки подается газ: азот, гелий, аргон, кислород или воздух. Он необходим для удаления расплавленного металла, поддержания его горения, охлаждения прилегающей зоны, увеличения скорости и глубины резки.
Процесс лазерной резки можно посмотреть на видео ниже:
У лазерной резки есть ряд достоинств:
- благодаря отсутствию контакта с поверхностью разрезаемого металла ее используют для работы с легкодеформируемыми или хрупкими материалами;
- с ее помощью можно изготавливать детали любой конфигурации;
- экономный расход листового металла за счет более плотной раскладки на листе;
- высокая скорость и точность;
- можно резать металлы толщиной до 30 мм.
Недостатками лазерной резки считаются высокое энергопотребление, дорогое оборудование.
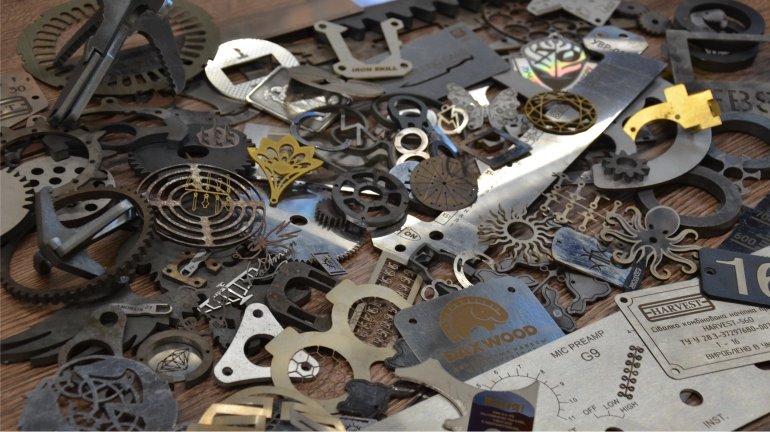
Лазерная резка оптимальна для изготовления сложных по конфигурации изделий из тонких металлов
Особенности плазменной резки
Для плазменной резки используют плазмообразующий газ: азот, кислород, смесь водорода с аргоном или сжатый воздух. В охлаждаемом плазмотроне он нагревается до температуры 5 000–30 000 °С и переходит в состояние плазмы: смеси нейтральных атомов, ионов и свободных электронов. В результате газ приобретает способность проводить электрический ток. За счет теплового расширения его объем увеличивается в 50–100 раз и он с огромной скоростью вытекает из плазмотрона. Под воздействием плазмы начинает плавиться металл.
Узнать больше о плазменной резке можно из видео ниже:
При использовании плазменной резки между электродом и соплом резака возникает электрическая дуга. Для этого используют источники питания постоянного тока. Дуга образуется при поднесении резака к материалу.
Различают аппараты прямого или косвенного действия. В первом случае дуга образуется между катодом плазматрона и разрезаемым материалом (плазменно-дуговая резка). Во втором – внутри резака (плазменно-струйная резка). Этот способ обработки удобен для материалов, не проводящих электрический ток.
Преимущества и недостатки плазменной резки
У плазменной резки 4 основных преимущества:
- Можно работать со сталями, алюминиевыми и медными сплавами, чугуном и прочими материалами.
- Можно изготавливать детали сложной конфигурации.
- Режет металл толщиной до 150 мм.
- Высокая точность.
К недостаткам плазменной резки относят необходимость механической обработки кромок разрезаемых материалов и конусность резов.
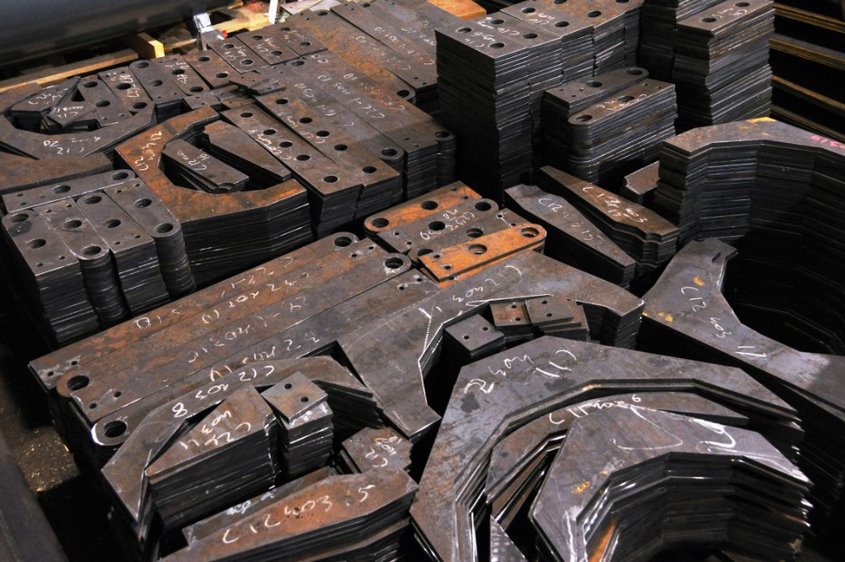
Плазменная резка чаще используется в машиностроении
Сравнение лазерной и плазменной резки
Можно выделить основные различия между лазерной и плазменной резкой.
- Плазменная резка эффективна при толщине материала 20–40 мм. Может использоваться для раскроя меди толщиной до 80 мм, чугуна – до 90 мм, алюминия и его сплавов – до 120 мм, легированных и углеродистых сталей – до 150 мм.
- Конусность реза. При лазерной резке металла толщиной более 6 мм появляется конусность кромок порядка 0,5°. По этой причине нижняя часть получаемых отверстий имеет увеличенный диаметр. Для плазменной резки этот параметр больше – 3–10°. При выполнении отверстий этим способом их выходной диаметр меньше входного.
- Температурное воздействие. Лазерная резка характеризуется малой зоной температурного воздействия. Плазменная резка воздействует на металлы высокой температурой, и листы толщиной до 0,5 мм могут покоробиться.
- Качество резки. По этому параметру лидер – лазерная резка. Для нее характерны стабильный и точный рез, а также отличное качество кромок. При использовании плазменной резки образуется окалина и нужна доработка кромок.
Лазерная резка — точность и чистота на тонколистовых деталях
- Лазер наводится точнее плазмы. Плазменная дуга нестабильна. Конечно, при правильной настройке она не начнет скакать по всему листу металла. Но плазма постоянно колеблется, делая углы и вырезы менее четкими. Для небольших деталей, особенно сложной формы, это критично. Лазер же режет металл четко там, куда его направили, и не двигается. Это принципиально для деталей, на которых требуется высокое качество и точное соответствие проекту.
- Лазер может делать более узкие прорези, чем плазма. Четкие отверстия при плазменной резке должны иметь диаметр в полтора раза больше толщины металла — и никак не меньше 4 мм. Лазер делает отверстия с диаметром, равным толщине металла — от 1 мм. Это расширяет ваши возможности при проектировании деталей и корпусов, развертки для которых режутся лазером.
- При лазерной резке тепловые деформации минимальны. Теоретически перегреть деталь можно даже лазером — если написать специальную издевательскую программу резки. Например, лазером не вырезают совсем мелкие и частые отверстия для вентиляции — от этого может произойти перегрев металла. Для лазерного раскроя вентиляционные отверстия делают более крупными и менее частым. В остальных случаях деформации от лазера не будут заметны. Плазма этим похвастаться не может — нагреваемая зона там шире и деформации более выражены. По этому показателю лазер снова дает более качественный результат, чем плазма.
- Лазер не оставляет окалины на тонколистовом металле. Значит, после лазерной резке развертки отправляются не на зачистку, а сразу на гибку. Это экономия рабочих часов на производстве деталей — а значит, и экономия денег заказчика в итоге.
- У отверстий, вырезанных лазером, более перпендикулярные кромки. Конусность отверстий — серьезная проблема плазменных станков. У лазерных станков при толщине металла до 4 миллиметров стенки будут оставаться перпендикулярными, а при толщине выше 4 миллиметров — получат легкий скос в районе 0,5 градуса, нижние отверстия будут получаться чуть больше по диаметру, чем верхние. При этом, однако, искажения их формы не будет, и верхние, и нижние отверстия останутся строго круглыми — а отверстия от плазмы при увеличении толщины металла начинают стремиться к эллиптической форме.
- У станков лазерной резки высокая скорость работы — но она высокая и у плазменных станков. Здесь оба метода хороши. И оба теряют скорость при увеличении толщины металла.
- Лазер неэффективен для металла средней и высокой толщины. Это главный его недостаток по сравнению с плазменной технологией. На толщинах от 20 до 40 миллиметров его применяют уже намного реже, а свыше 40 миллиметров — вообще практически не используют.
Плазменная резка — ниже качество, больше свободы по толщине
- Большая свобода по толщине металла для резки — главное преимущество плазмы по сравнению с лазером. Плазменную резку уместно использовать для:
- стали толщиной до 150 миллиметров;
- чугуна толщиной до 90 миллиметров;
- алюминия толщиной до 120 миллиметров;
- меди толщиной до 80 миллиметров.
- Высокая скорость работы — как уже было сказано, это общий плюс для обоих видов.
- Конусные отверстия. Это обязательно нужно учитывать при выборе плазменной резки. И если такая неаккуратность отверстий недопустима для конкретного заказа — лучше разрезать его лазером. Стенки отверстия при плазменной резке отклоняются от вертикали на 3–10 градусов. У лазера, напомню — 0,5 градуса. В отличие от лазера, плазма делает нижнее отверстие более узким, чем верхнее. Если толщина металла около 20 миллиметров, то разница между верхним и нижним диаметрами реза может превышать 1 миллиметр.
- Меньшая точность, более широкие минимальные прорези относительно толщины металла, увеличенные тепловые деформации — противоположность всего того, в чем лазер хорош.
- Часто формируется окалина. Стоит сказать, что окалина от плазменной резки снимается с металла достаточно легко — однако ее все‑таки придется снимать, а это расход человеко‑часов и соответствующее увеличение себестоимости производства.
- Стоимость плазменной резки быстро увеличивается с увеличением количества отверстий на одну деталь. Это связано с тем, что расходные элементы плазменных установок служат определенное количество циклов «включение‑выключение». Наличие в развертке окон увеличивает износ расходников — и это приходится учитывать в себестоимости резки. Расходники лазерных станков меньше зависят от циклов «включение‑выключение» — соответственно, прорезание в развертке окон меньше влияет на стоимость часа работы.
Сводная таблица — сравнение резки металла лазером и плазмой
Лазерная резка | Плазменная резка | |
---|---|---|
Ширина реза | Постоянная — от 0,2 до 0,375 миллиметра | Непостоянная из‑за нестабильности дуги — от 0,8 до 1,5 миллиметра |
Точность резки | ±0,05 миллиметра | От ±0,1 до ±0,5 миллиметра в зависимости от изношенности расходников |
Конусность | Менее 1 градуса | От 3 до 10 градусов |
Минимальные отверстия | Диаметр примерно равен толщине металла | Диаметр примерно в 1,5 раза превышает толщину металла и не должен быть меньше 4 миллиметров. |
Внутренние углы | Точные | Немного скругленные |
Окалина | Почти не встречается | Легкая, но присутствует почти всегда |
Прижоги | Незаметны | Заметны на наружных кромках |
Тепловое воздействие | Незначительное | Увеличенное по сравнению с лазером |
Оба конкурирующих вида резки — достойные и нужные. Нельзя сказать, что один из них универсально лучше другого. Каждый из них выгодно подходит для своих задач — нужно понимать различия и использовать каждый по назначению, чтобы не терять качество деталей и не переплачивать за них.
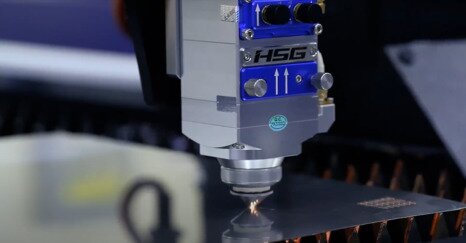
Производительность процесса
Зависит в первую очередь от материала и его толщины. Лазерная резка может использоваться и для обработки нержавеющей и низкоуглеродистой стали, меди, латуни, алюминия, титана, акрила, пластика, стекла, дерева, кожи, текстиля. Плазморезы могут работать только с металлами, проводящими электричество.
По-разному показывает себя лазерная и плазменная резка и при работе с металлами различной толщины. При обработке тонкого листового материала (до 6 мм), особенно при высоких объемах работ и формировании сложных контуров, выигрывает лазер. Если толщина металла будет более 6 мм, то у лазерного станка скорость обработки будет сопоставима с плазмой, но качество лазерной резки будет выше. У лазерной обработки отсутствует конусность, которая присуща плазменной резке. А вот при работе с заготовками более 30 мм плазменные станки справляются лучше, но такие заготовки имеют высокую конусность и нуждаются в последующей обработке.
Качество реза
От качества реза зависит не только внешний вид готового изделия, но и сложность последующей обработки. И здесь лазерная резка металла существенно превосходит показатели плазменной резки. Заготовки, полученные с ее помощью, нуждаются в минимальной финишной обработке. Шероховатость поверхности составляет всего 1,25-2,5 мкм, а конусность кромки – 0-20. Детали, полученные на плазменном станке, необходимо будет дополнительно шлифовать (и поверхность, и кромку), снимать окалину. Соответственно шероховатость поверхности и конусность кромки в этом случае составляют 6,3-12,5 мкм и 0-100.
И здесь надо сделать выбор в пользу продуктивности процесса или качества реза, а также смотреть, с какими запчастями предстоит работать. В частности, основное требование при изготовлении приварного фланца – плоскость поверхности, а пережог кромки, шероховатость, конусность – это уже второстепенные показатели. А вот при производстве сложных деталей внимание уделяется именно качеству реза.
Основные отличия лазерной резки от плазменной приведены в таблице:
Параметр | Резка лазером | Плазменная резка |
Минимально возможный диаметр отверстия | 0,3-0,4 толщины материала | 0,9-,1,4 толщины материала, но не менее 2-3 мм |
Ширина реза | От 0,2 до 0,375 мм, остается стабильной | От 0,8 до 1,5 мм, но меняется ввиду нестабильности дуги |
Точность реза | Тонкий, с отклонениями в диапазоне 0,05 мм | В пределах 0,1-0,5 мм |
Вырезание внутренних углов | Возможно, с высокой точностью | Возможно, но только с радиусом |
Температурное воздействие | Минимальная зона термического влияния | Большая зона термического влияния приводит к деформациям и короблениям |
Себестоимость процесса резки и стоимость эксплуатации
Изначально отметим, что станки для лазерной резки обойдутся примерно в 4-6 раз дороже плазменных станков. Стоимость их эксплуатации зависит от ряда параметров:
- Затрат электроэнергии и рабочих газов. При резке тонкого металла энергопотребление обоих видов станков примерно одинаковое. Чем больше толщина материала, тем больших затрат будет требовать лазер.
- Сервисное обслуживание, затраты на ремонт. Лазерное оборудование редко выходит из строя, особенно при соблюдении эксплуатационных рекомендаций производителя. В плазменных станках требуется более частое обслуживание рабочей поверхности, т.к. удаляется большее количество материала, чем при лазерной резке.
Точно назвать себестоимость продукции и сроки окупаемости того или иного станка нельзя, ведь все зависит от особенностей производства, предстоящих задач.
Расходы на покупку и эксплуатацию
Стоимость станков имеет важное значение. Плазменные агрегаты доступнее лазерных, но стоит учитывать и затраты на их обслуживание и ремонт.
В процессе лазерной резки используются в основном такие газы, как воздух, кислород и азот. Энергетические расходы подразумевают затраты на электроэнергию, за счет которой питается установка, лазер и устройство, ответственное за охлаждение. К расходуемым материалам относятся: оптика, линзы, фильтры. Производить обновление компонентов в таких станках следует с различной периодичностью, зависит это от параметров и условий эксплуатации.
Плазменная резка осуществляется за счет воздуха и кислорода. Электроэнергия в данном случае обеспечивает работоспособность установки, без нее не обходится и процесс создания плазмы. Компонентов при такой резке используется немало, к ним относятся: сопло, электрод, крышки, экран и пр. На эксплуатационную стоимость влияет и количество отверстий, прошиваемых для резки – чем их больше, тем выше затраты.

Сделать правильный выбор в пользу того или иного станка можно только за счет глубокого анализа производства, а именно его задач и возможностей. Кроме того, необходимо рассмотреть вариант внедрения станков в существующие процессы или перестройки этих процессов, обеспечив таким образом наиболее эффективное использование лазерной или плазменной резки.
Важным отличием плазменной резки является простота в ее освоении. Особенно хорошо она подходит для тонкопрофильных металлов. Если же толщина реза превышает 2.5 миллиметра, тогда возникает необходимость в использовании мощных источников питания, что невыгодно.
Лазерное оборудование позволяет решать более широкий спектр задач. С его использованием можно выполнять разметку, маркировку, формировать отверстия и т.д. Что касается срока службы лазерных агрегатов, то они несравнимо больше, чем у плазменных.
Технологии лазерной и плазменной резки металла получили широкое распространение в современной промышленности. Они позволяют обеспечить высокую производительность, а также хорошее качество выполняемых работ.
В зависимости от поставленных целей каждая технология облает своими преимуществами, хотя во многих случаях они могут быть взаимозаменяемыми.
- Волноводный уровнемер: как выбрать и внедрить
- Отремонтировать авто в Санкт‑Петербурге недорого: возможно ли это?
- С помощью какого оборудования проводят лазерную резку металла?
- Преимущества ручных лебёдок МТМ: надёжность, универсальность, цена
- Практическое руководство по очистке и восстановлению металлических деталей